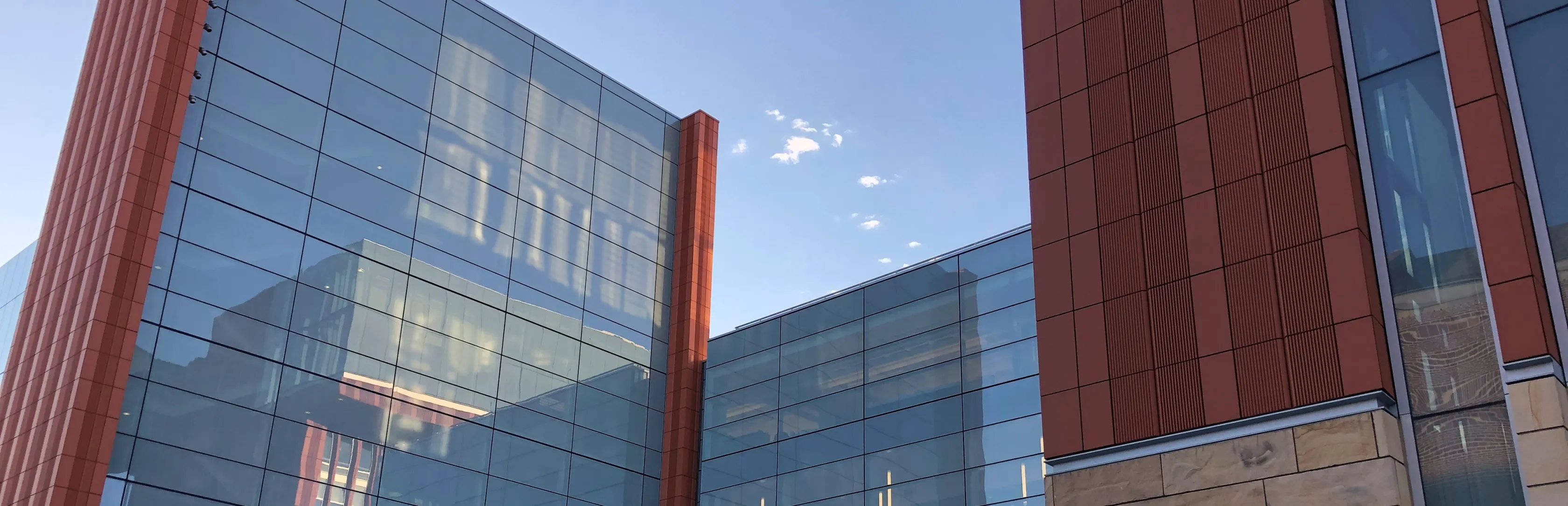
News
Welcome to Tauber Institute for Global Operations News.
Explore our press releases, feature articles, and announcements about Tauber students, speakers, team projects, and events.
Welcome to Tauber Institute for Global Operations News.
Explore our press releases, feature articles, and announcements about Tauber students, speakers, team projects, and events.
A Tauber Institute team project puts your average internship to the test. You won’t be stuffing envelopes or setting up your boss’ Gmail account. Instead of fetching coffee, you might be asked to calculate the potential cost-savings of installing an in-house coffee machine vs. going to a shop. Tauber teams are recruited to tackle real business challenges and implement sustainable improvements. Team members are not seen as interns, they’re seen as problem-solvers, and some of the country’s leading companies call on them for help.
One of these companies is Precision Castparts Corp. (PCC), a multi-billion dollar manufacturer of cast metal parts for aerospace, industrial, defense, and automobile technologies. PCC’s factories span the globe, and in order for the company to continue performing at top level, each factory must consistently meet customer demand. Unfortunately, one of PCC’s factories, PCC Fasteners in Jenkintown, PA, was continually coming up short.
“Before we got there, they’d make 1000 parts and end up with 800,” says Elizabeth Hershman, an MBA candidate at the Ross School of Business and one of two team members on the project. “They were losing above what they anticipated.”
“The factory had no way to know if they were going to make the customer demanded order quantity until the parts were packed,” says David Moore, an MSE-ME candidate in the College of Engineering and team member number two. (David is also a Rhodes Scholar recipient. Read more here).
Due to the lengthy production process and high volume of orders, losing parts is expected in this type of factory environment. As long as a factory can accurately measures its yield, it will stay in the green. Unfortunately, PCC Fasteners was miscalculating the yield, and thus losing more parts than they anticipated. According to Hershman and Moore, this amounted to a $20M problem.
With the project’s scope fully illuminated, Hershman and Moore got to work. “Our goal was to design a tool kit that can be used to track the yield of the orders and display information on where yield loss occurs within the plant,” says Moore. “We worked with the operators to have them enter in the number of bad pieces they produce each shift, and then we wrote a program that collects this information and displays it in a useful way.”
Once Hershman and Moore created the new yield tracking system, they assumed the next step – deployment – would be relatively straightforward. But in a high-stakes, multi-party environment like PCC Fasteners, they were not just dealing with numbers, they were dealing with people.
The PCC Fastener factory is over a century old, and the average employee tenure is 35 years. “Most of the workforce had seen multiple management changes and multiple initiatives started,” recalls Hershman. “It was hard to convince them that we had a new idea that would work, because they had seen so many ideas that came before fail.”
The team was now faced with a new obstacle: in order to properly implement the new yield tracking system, they needed the factory’s entire workforce on board. Hershman and Moore realized that to win over the employees, they needed to prove that their strategy worked.
“We started small,” says Hershman. “We had two groups of people on each product line who were willing to test out the new system.”
As anticipated, the system proved extremely successful, so Hershman and Moore took the results and presented them to the rest of the employees.
“When they saw the opportunity to make that improvement and save thousands,” continues Hershman, “that was the point that other people were willing to buy in.”
Support grew quickly, and the new yield tracking system was deployed factory-wide. After years of empty promises and millions of dollars wasted, two students from the Tauber Institute had managed to make a real difference.
“Our project has received a lot of attention,” says Moore. “It is really exciting to see something we have worked so hard on really take off and have complete buy in from the operators up to the President of the Division.”
Looking back on her time at PCC, Hershman sums up her experience: “I think one of the best things is that during our internship, we got a real problem that had a real impact on the company and a real opportunity for us. Not just a normal internship where you do more menial tasks. It was up to us to drive the project.”
View photos from Spotlight! 2014
Read 2014 Spotlight! Book
Written by: Joshua Kraus
About Tauber Institute for Global Operations
The Tauber Institute for Global Operations is a joint venture between the University of Michigan’s Stephen M. Ross School of Business and the College of Engineering, and 30 industry partners to facilitate cross-disciplinary education in global operations management. In addition to broad array of core and elective courses, the innovative LeadershipAdvantageSM Program provides students with the tools to ascend to major operations leadership roles. Well-designed and managed team projects form the cornerstone of the Tauber Institute experience and allow students to apply their knowledge to real world settings. http://www.tauber.umich.edu
Contact:
Theresa Ceccarelli, 734-647-0308, [email protected]