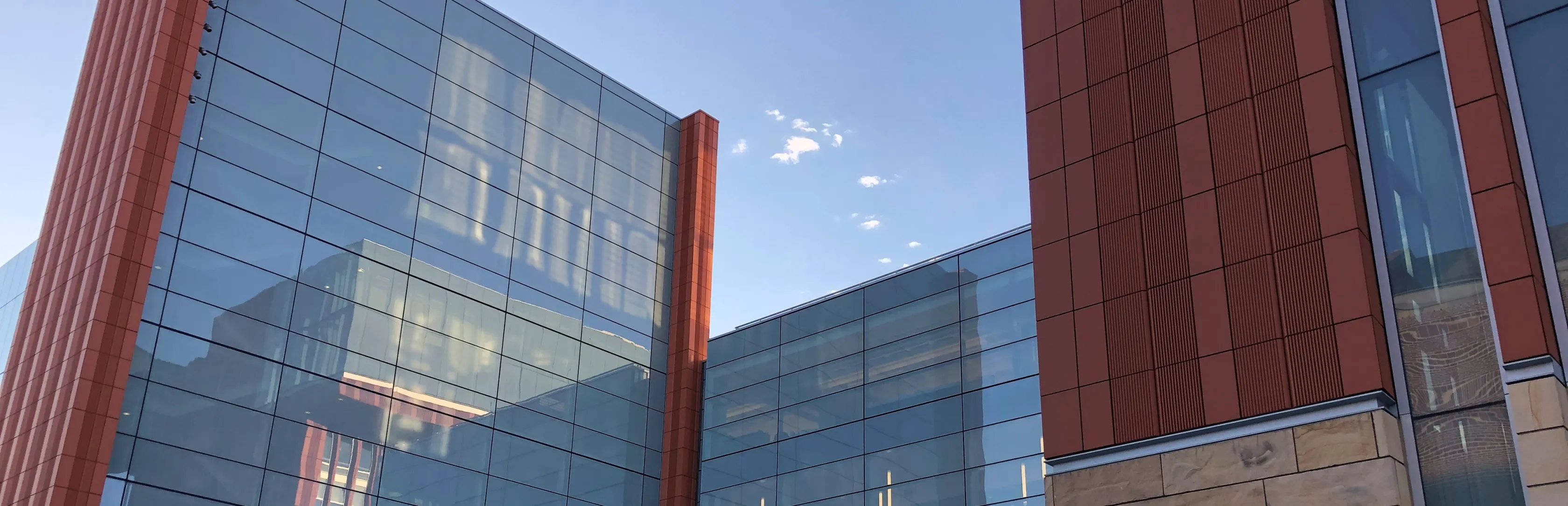
News
Welcome to Tauber Institute for Global Operations News.
Explore our press releases, feature articles, and announcements about Tauber students, speakers, team projects, and events.
Welcome to Tauber Institute for Global Operations News.
Explore our press releases, feature articles, and announcements about Tauber students, speakers, team projects, and events.
First described in science fiction in the mid-1940s, 3D printing is now providing solutions to real-world manufacturing problems. A Tauber Team developed a plan for Cummins, Inc., to integrate 3D manufacturing into its cross-functional no-source order-fulfillment process.
While technologies like those used in cell phones render equipment obsolete at a breakneck pace, some industries face challenges at the other end of the spectrum: diesel engines are designed to last for decades, but as new models are introduced, it can be difficult for manufacturers to provide replacements for no-source parts (components for which vendors no longer exist).
In mid-2018, Cummins, Inc., a Fortune 500 company that designs, manufactures, distributes, and services diesel and alternative fuel engines and related components, brought a Tauber team to its Columbus, Indiana, headquarters to integrate 3D printing—additive manufacturing—into its cross-functional no-source order-fulfillment process.
The three-person Tauber team worked with the Cummins New & ReConditioned Parts (NRP) division, which supports the aftermarket supply chain for over 200,000 current and legacy parts. Advait Bhogte (Master of Engineering in Manufacturing), Makura Compton (Master of Business Administration), and Dieon Roger (MSE Mechanical Engineering & MEng Systems Engineering & Design) came to the project at Cummins with varying levels of experience with 3D printing, a technology that emerged in the mid-1980s and has become increasingly prevalent in the last couple of decades. The scope of work, however, was much more about an analysis of process than a focus on engineering or technology. The team began by interviewing stakeholders in multiple rounds. These invaluable conversations informed their analysis of the current process flow and construction of value stream maps: Where were the opportunities to optimize the process?
Increased Customer Satisfaction and Decreased Costs
Cummins can use the process the Tauber team developed to improve efficiency and customer satisfaction through shorter lead times on fulfillment of no-source orders for qualified parts. The new process will also reduce labor hours, the number of required information systems, and the number of decision points and cross-functional handoffs embedded in the process. According to a cost model the team built, using conventional suppliers to resolve no-source cases incurred annual indirect costs of approximately $1M. NRP’s business case for using 3D printing was strengthened because the lower indirect costs can offset any higher per-unit direct costs of additive manufacturing.
Navigating the Process
Advait Bhogte, Makura Compton, and Dieon Roger all described stakeholder interviews and mapping the existing process as the most challenging aspects of their work. They also noted that the scope of work shifted more than once during their fourteen-week stint, particularly after the mid-project review, requiring a flexible, nimble response. The fluid nature of the project is not surprising given that, as Roger noted, no one in the diesel engine industry had yet used 3D printing to address no-source parts production before.
Bhogte noted that the stakeholder interviews conducted with five different departments revealed that “the process varied significantly across business units, which made it challenging to document and understand the key decision points and bottlenecks in the existing process.” Compton said, “The biggest challenge was mapping the process in the level of detail that we needed to properly analyze it . . . Fortunately we were well-supported by the stakeholders that carried out the processes each day with whom we conducted many hours of whiteboard sessions.” Round 1 interviews focused on mapping out the process, while Round 2 comprised execution-level detail and quantifying how the process was performing. The team could then support their final process improvement recommendations with metrics that mattered to Cummins. Software tools like Excel financial modeling and Tableau for data analysis also played a part in crafting the team’s recommendations as they took a deep dive into process, while creating an affinity diagram using dozens of sticky notes on a wall allowed the team to manage and categorize data.
The team recognized the great support they got from faculty members and support staff at Tauber itself, particularly in developing the cost model for the existing process. Danguole Kviklys at Michigan Ross Kresge Library created a set of articles on 3D printing and other resources for the team. Professor of Technology and Operations and Tauber Institute Co-Director Damian Beil met with the team every week, providing invaluable insights and feedback. Faculty advisors M.S. Krishnan of Michigan Ross and Brian Love from the School of Engineering contributed important perspective throughout the project, giving guidance on the process, providing a sounding board, and managing expectations of both the sponsor team at Cummins and the student team.
Team Benefits
The project at Cummins provided the team with a comprehensive look at the additive manufacturing process and an understanding of cost modeling; experience in practical problem solving, project scoping, and value stream mapping; and experience working with different kinds of tech groups cross functionally.
Roger enjoyed being able to leverage his education while also gaining an understanding of implications of using additive manufacturing for different applications. He noted that the project gave a very high-level view of the end-to-end process in meeting a customer's need.
Bhogte appreciated gaining “a deep understanding of the additive manufacturing process, types of it, and its advantages and limitation. It also helped me understand ways of cost modelling and how to calculate total cost of a product.”
Compton summed up the team’s experience working on the Cummins project with, “There is no substitute for participating in real-world problem solving of this manner and magnitude in the function in which you plan to build a career.”
Cummins, Inc. Team
Student Team
Advait Bhogte – Master of Engineering in Manufacturing
Makura Compton – Master of Business Administration
Dieon Roger – MSE Mechanical Engineering & MEng Systems Engineering & Design
Project Sponsors
Nikhil Doiphode – Parts Research & Technology Engineer, New & ReCon Parts
Brent Lollar – Director of Marketing Operations, New & ReCon Parts
Kelly Schmitz – Executive Director of Engineering, New & ReCon Parts
Todd Wieland – Director of Research & Technology, New & ReCon Parts
Faculty Advisors
M.S. Krishnan – Ross School of Business
Brian Love – College of Engineering
About Tauber Team Projects
Each two- to three-person Tauber Team consists of graduate students in Engineering, MBA, and/or MSCM programs. Along with receiving high-level corporate support from the sponsoring company, each team is advised by a College of Engineering and a Ross School of Business faculty member, and overseen by a Tauber Institute Co-Director. The projects begin on-site in May and continue for 14 weeks. Students present the results of their projects and compete for over $40,000 in scholarships at the U-M Tauber Institute’s annual Spotlight! event, held each September in Ann Arbor, Michigan. Spotlight! provides outstanding opportunities for students and corporate partners to establish relationships while exploring innovations in operations and manufacturing.
The 2018 Tauber Team Projects resulted in $564.4 million in savings according to sponsoring company calculations, an average of $28 million per project over three years.
To learn more about the Tauber Institute for Global Operations, visit http://www.tauber.umich.edu/ or call us at (734) 647-1333.